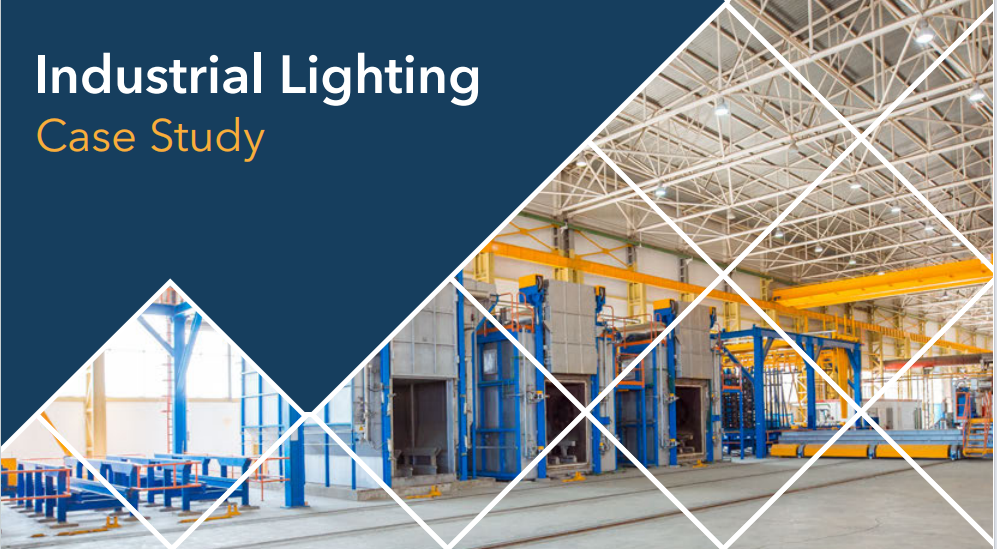
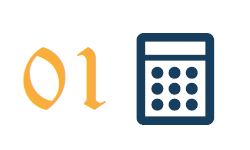
More Energy Saving
Reduce installation, set up and training time by using the Morstar wireless system that includes luminaires and controls.
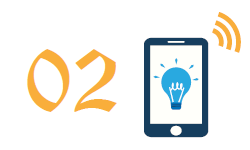
More Simple
Automatic control is designed to ensure cost savings, while manual control cannot achieve the ame
reliability.
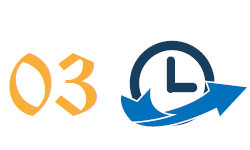
More Save time
It is simpler to better manage and fully optimize your lighting projects by using the Morstar mobile App.
How Smart Industrial Lighting Can Help You Become a Better Manager
As you know, light is important to people’s well-being, health and performance. A modern, highly effcient lighting system saves a lot of energy, so managers need an energy-saving lighting solution. The well designed, energy effcient lighting plays an important role– providing good quality, uniform illumination throughout the workspace.
From rough machining workshops, large processing plants and warehouses through automotive engineering: the requirements for industrial lighting are as complex as the work tasks and the operating environments. Work processes are becoming increasingly complex and the lighting needs to accom- modate a wide variety of visual tasks.
Morstar has the LED lighting solutions for such environments that can be individually matched to different lighting situations, meeting your needs for the moment.
The need for a suitable lighting scheme is due to the unique character of industrial buildings and conforms to the following needs:
- Human Centric Lighting
- Improve Work Productivity
- Reduce Maintenance Costs
- Refresh The Operational Effciency of a Given Space
- Improve Workers’ Safety as Well as Their Working Conditions
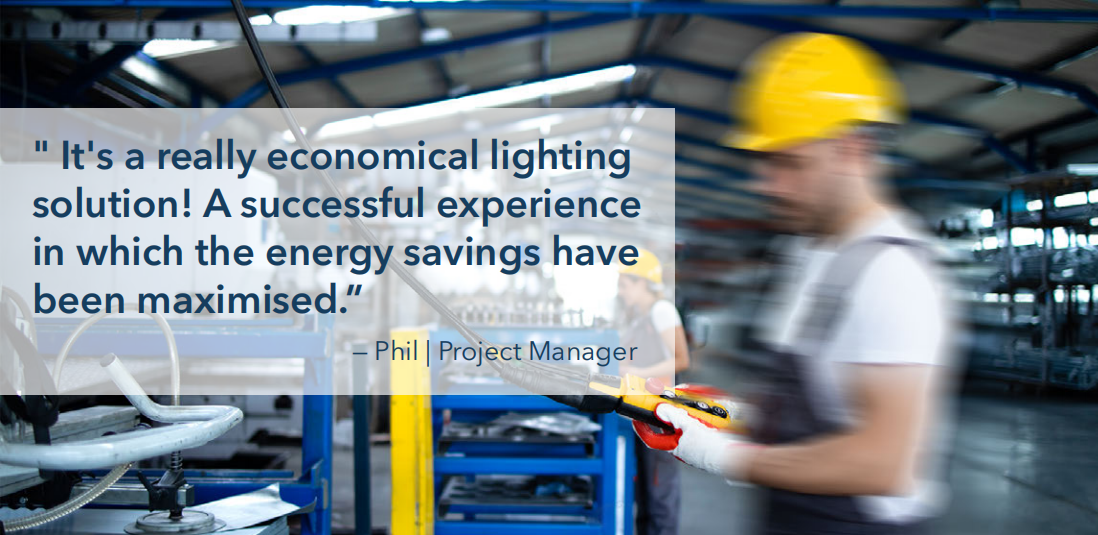
“Phil is a project manager at a processing plant. The plant in Detroit is still using a large number of fluorescent tubes. This troubled Phil, “Now that the fluorescent lamp has reached the end of its life cycle, we need a new solution, a reliable and energy-saving solution.”

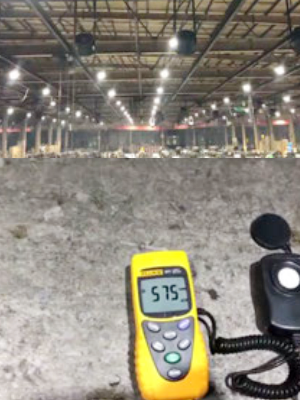
Before Transformation
Challenge: The workshop uses sensor lights without dimming function, with an average illuminance of 135Lx. The workshop lighting cannot be controlled by area, and the daily electricity consumption is huge. When the fault cannot be accurately located, a lot of manpower and time costs are consumed.
After Transformation
Solution: The workshop lighting uses LED High Bay Light/ LED Vapor Tight Light, each set of luminaires is equipped with a Bluetooth controller, and the site is equipped with a gateway and router. The average illuminance was 575Lx.
In harsh industrial workplaces, a good lighting environment can reduce the rate of work errors and reduce the probability of nonconforming products. A suitable lighting environment can help workers concentrate and improve production effciency. And after improving the safety of work, you can reduce the occurrence of safety accidents. Finally, while meeting the requirements of working face lighting, energy consumption needs to be reduced.
“We should choose reliable lighting fixtures that are insulating, corrosive, waterproof and dustproof.” Richard, lighting designer of Morstar, made a field visit to the factory and proposed his own solution according to the characteristics of Phil’s products. “The use of LED mining lights or triple-proof lights can meet the requirements of durability and reliability.”
Morstar is a lighting manufacturer with 22 years of experience. In addition to high quality lamps, Morstar also provides Human-Centric lighting solutions. LED High Bay Light and LED Vapor Tight Light selected by Richard are the Morstar’s star products. The transformed lighting project aims at energy saving, cost reduction and intelligent effeciency enhancement, meeting intelligent control functions such as area control, dimming control, timing control, energy consumption and fault statistics, and combining with the SaaS system to provide customers with convenient management and operation.
Morstar sustainable lighting solutions can create a more efficient and productive workplace by providing better lighting that ensures task areas are well lit and have high visual comfort, helping to reduce mistakes and boost production. Please read the table below for the recommended parameter levels for various manufacyuring lighting requirements.
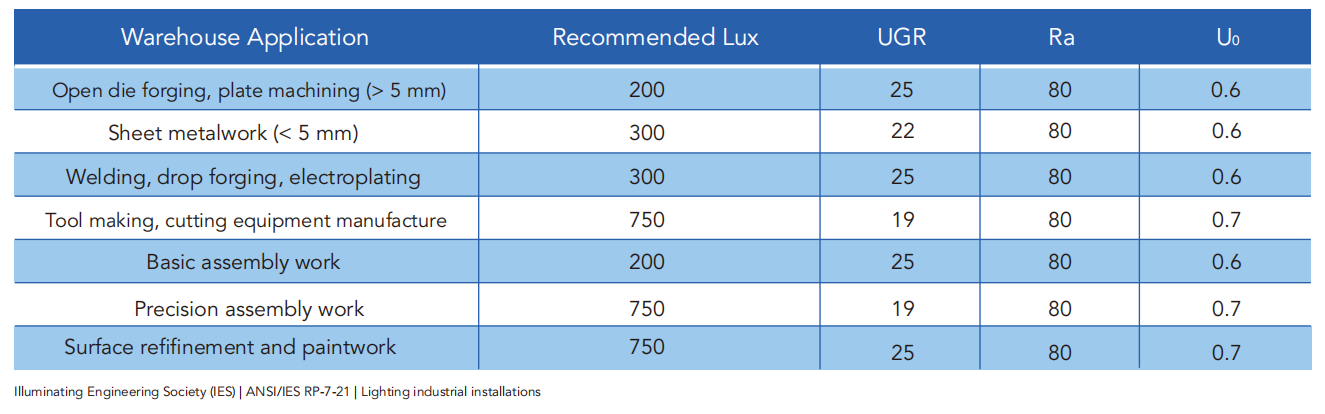
The visual task requirements vary along with the wide range of activities performed: the simple visual tasks include basic assembly and forging work, whereas welding and medium-fine machine work present higher demands. The eyes are challenged to the maximum during high-precision work on machines, for soldering and at control and measuring stations. Typically, factories are large buildings where we apply for a general illumination scheme. However, for specific tasks that require high standards and specific requirements, it is necessary to apply an independent lighting solution. It must be a comfortable lighting experience for the user.

After inspection and calculation, Morstar’s lighting designer Richard divided the entire plant into three different functional areas A/B/C. Area A is the finishing
workshop (required illuminance 500 lux), area B is the rough processing workshop ( required illuminance 300 lux), and area C is a raw material warehouse (required illuminance is 200 lux).
The advantage of sub-regions is that it is convenient for operators to manage and make corresponding operations to maximize energy conservation.
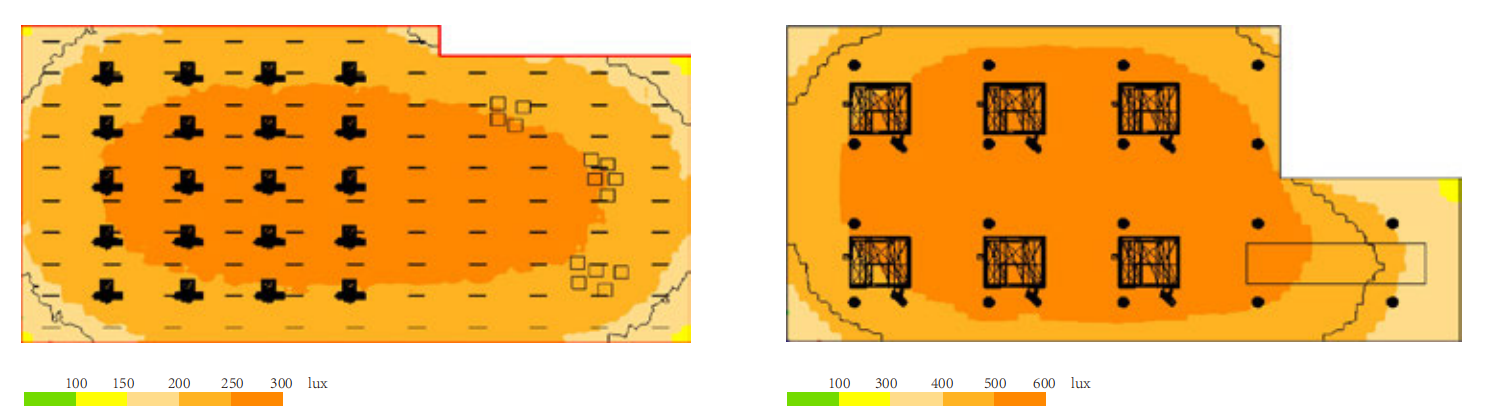
The height of Phil’s plant is 12 meters. Morstar uses 200W LED High Bay Light and 40W LED Vapor Tight Light when doing lighting renovations, and is equipped with a smart Bluetooth control module. After adding factory drawings and lamps through the SaaS system, Richard adjusted the power and brightness of the products according to the actual requirements of different areas.
Through the on-site switch panel, we classified and added the lamps and lanterns in Area A, Area B, and Area C, so that one APP can control the lighting fixtures in the area, and set the brightness in multiple modes ( working mode brightness is 100%, energy-saving mode brightness is 50%- 75%, noon break mode brightness is 25%, off-duty mode brightness is 10% or turn off).
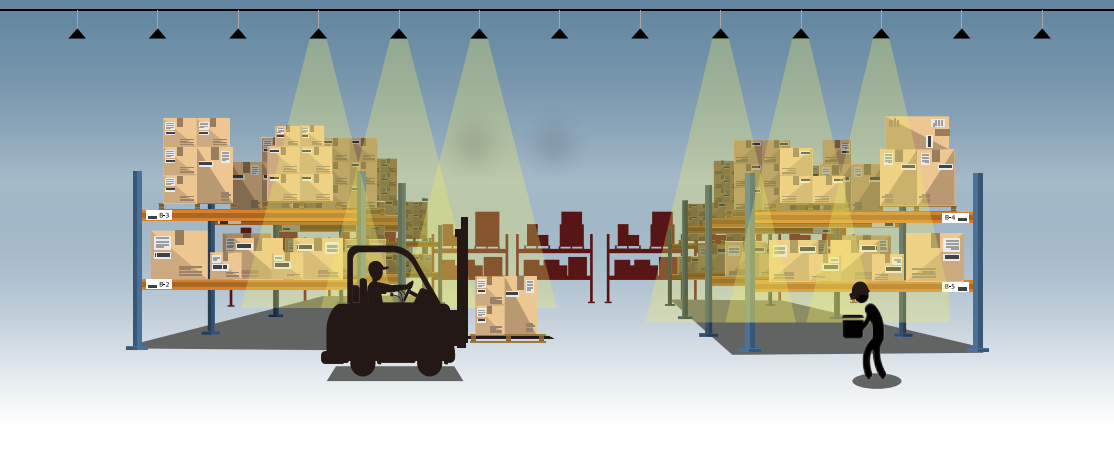
It is necessary to avoid the generation of large amounts of ineffective lighting for industry lighting. Leaving the lighting on when they are vacant is costly and unnecessary. The lighting need only be on when the workbenches are occupied or the warehouse lighting is only opened for people/ forklift traffic. By simply combining the luminaires over the area with a Bluetooth sensor, the sensor over that luminaires will detect when someone is there and switch the light on. Once that person/ forklift leaves, after a set time, the lighting will be switched off completely, allowing savings related to energy, maintenance and carbon emissions to be realised.
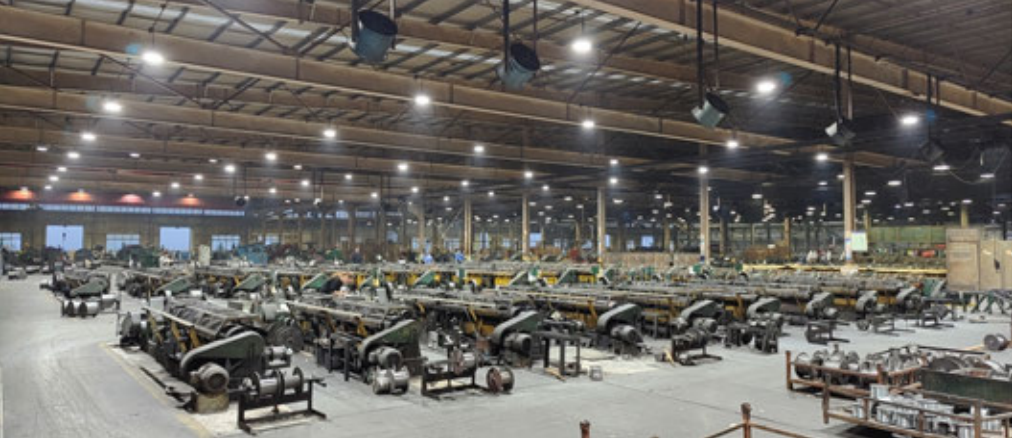
In the industry 4.0 era, human needs are very important, and the theme of “Human Centric Lighting” is gaining in significance. The flexible adjustment of modern lighting systems, from the assembly plant to the logistics center, can meet the requirements of various work fields. It benefits from smart lighting: innovative sensor technology, which can automatically adapt to the presence, users and activities, taking into account the visual, emotional and physiological needs of people working during the day and night. This is why the lighting renovation of Phil’s 26,900 square foot factory was so successful
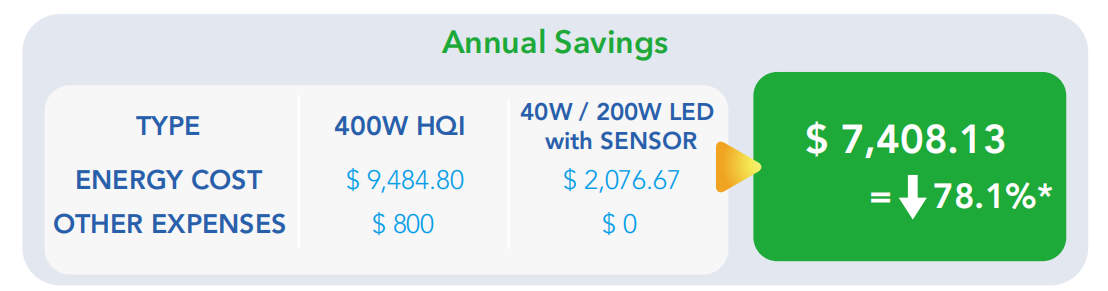
*Figures are based on the conversion from 400W HQI luminaires operating 4,229h (16 hours/day x 6 days/week x 52 weeks) to 200W LED High Bay Light and LED Vapor Tight Light with dimming occupancy sensors. Costs assume $0.10/kWh utility rate. $800is the cost of the ballast. The lighting system with integrated sensors can save up to 78.1% of the old warehouse lighting energy consumption.
The high energy efficiency of the 400 series LED high bay light and 451 series vapor tight light allows for energy savings of up to 78.1% compared with the old lighting system. The connected load was reduced by 66.3% from 19,000W to just 6,400W. The smart lighting control system allowed for additional electricity savings of up to 11.8% thanks to the Bluetooth control module and integrated sensors. Employees also benefit from the new lighting due to better quality lighting and excellent colour reproduction. Changing the lighting system from traditional high voltage sodium lamp to LED coupled with lighting controls resulted in impressive savings for Phil, at least amount to an impressive $ 7,408.13 p.a.